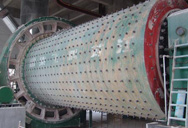
Recent Advances in Ball-Milled Materials and Their
2024年6月7日 Ball milling has the capacity to change materials’ crystal structure, specific surface areas, pore volumes, and particle sizes and even promote grafting reactions to obtain functional groups to surfaces. This
More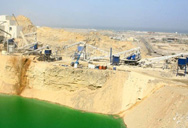
Direct Mechanocatalysis: Using Milling Balls as Catalysts
2020年4月21日 High-speed ball-milling: Direct mechanocatalysis is a new catalysis concept using high speed ball milling conditions. The surface of the milling balls is the catalytic active
More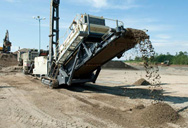
A Review of the Grinding Media in Ball Mills for Mineral Processing
2023年10月27日 Grinding media play an important role in the comminution of mineral ores in these mills. This work reviews the application of balls in mineral processing as a function of the
More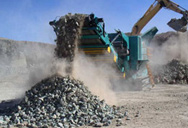
Ball mill - Wikipedia
A ball mill is a type of grinder filled with grinding balls, used to grind or blend materials for use in mineral dressing processes, paints, pyrotechnics, ceramics, and selective laser sintering. It works on the principle of impact and attrition: size reduction is done by impact as the balls drop from near the top of the shell. A ball mill consists of a hollow cylindrical shell rotating about its axis. The axi
More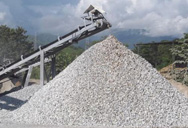
Ball Mill - an overview ScienceDirect Topics
A ball mill is a tumbling mill that utilizes steel balls as grinding media to grind materials. It can operate either wet or dry, with the capacity to produce products in the order of 100 μm, making
More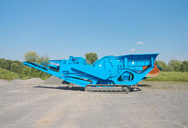
Relationship between the ball-milling time and the specific surface ...
Figure 5 shows that the specific surface area of the sample before ball milling was 148 m²/g and the values of the ball-milled samples were between approximately 270 m²/g and 315 m²/g.
More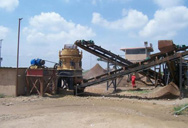
A comparative study on a newly designed ball mill and the
2020年1月1日 A study of the laboratory ball mill performance for different mill speeds operating with and without lifters (cap open and cap close) at the discharge end has been presented in
More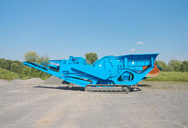
Cross-section of typical ball mills showing various ... - ResearchGate
The ball mill is a rotating cylindrical vessel with grinding media inside, which is responsible for breaking the ore particles. Grinding media play an important role in the comminution of...
More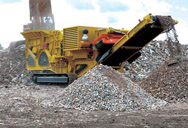
Ball Mill - SpringerLink
2024年1月1日 Ball mill is the key equipment for crushing materials after they are crushed. It is widely used in cement, silicate products, new building materials, refractories, chemical
More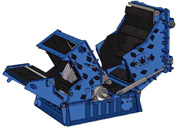
Ball Mill Liner Design - 911Metallurgist
2016年1月5日 Mill HEAD LINERS. Head liners are of the segmental type constructed of Manganese Steel, Chrome molybdenum, or Ni-Hard and are designed to pass easily through the manhole opening or discharge opening in
More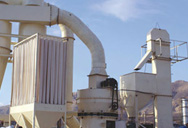
(PDF) Grinding Media in Ball Mills-A Review - ResearchGate
2023年4月23日 One of the most used tumbling mills is the ball mill. This paper reviews different types of grinding media that have been developed and improved over the years and their properties.
More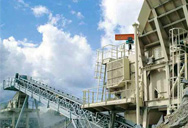
Ball Nose End Mill [Easy Guide to Ball Cutters] - CNCCookbook
2024年7月16日 Ball End Mills are always center cutting, so they can cut everywhere on the ball. We can think of them as a special case of corner radius endmills, where the corner radius is as big as it can be. ... ball noses are a tip type for end mills: And there is a Surface Finish mini-calc to help you determine scallop size calculations:
More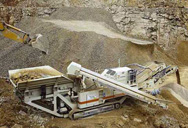
STEEL MILLING BALLS FOR BALL MILLS - Energosteel. Grinding Media Ball ...
3.1 The ball mill The device with a rotating drum filled by grinding balls and shredded material for materials crushing. 3.2 The grinding balls Products with ball form for material crushing in ball mills by abrasion, impact and crushing. 3.3 The conditional ball diameter Ball diameter rounded to standard values. 3.4 The nominal ball diameter
More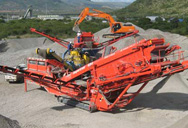
Grinding Media Lining Media Liner Wear Rate Modelling
2016年11月12日 Again insofar as the curve of Fig. 8.4 may be replaced by a straight line over this range, it also leads to the fairly generally accepted conclusion that the rate of wear is proportional to the power absorbed in a mill. Thus it appears that the ball wear is, very roughly, proportional to both rate of production of surface and to power input to ...
More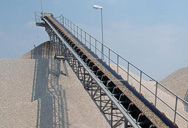
Effect of Milling Time on Particle Size and Surface Morphology
2013年9月1日 The ball milling successfully reduced the particle size from 323.7 nm (La(OH) 3 initial powders) to 173.4 nm (sample MT-159). The reduced particle or crystallite size after ball-milling is also ...
More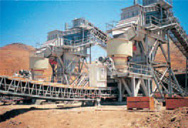
Ball Mill Design/Power Calculation - 911Metallurgist
2015年6月19日 The basic parameters used in ball mill design (power calculations), rod mill or any tumbling mill sizing are; material to be ground, characteristics, Bond Work Index, bulk density, specific density, desired mill tonnage capacity DTPH, operating % solids or pulp density, feed size as F80 and maximum ‘chunk size’, product size as P80 and maximum and finally the type of
More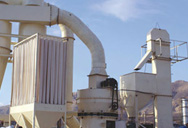
A tool wear prediction method for free-form surface machining of ball
Ball-end mills are commonly employed for semi-finishing and finishing of complex surfaces, widely utilized in the energy, automotive, aerospace and other industries. During surface machining, cutter workpiece engagement (CWE) area of the ball-end mill continuously varies with surface characteristics and the tool paths.
More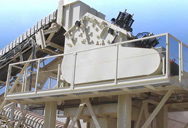
Effects of Mill Speed and Air Classifier Speed on Performance of
2021年6月29日 Nowadays, ball mills are widely used in cement plants to grind clinker and gypsum to produce cement. The research focuses on the mill speed as well as air classifier speed effect on the two ...
More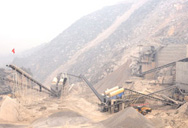
Ball Mill - an overview ScienceDirect Topics
A ball mill is a type of grinder containing various metal balls of different sizes that work on the principle of impact and attrition. From: Bioresource Technology, 2022. ... The inner surface area of the chamber is lined with an abrasion-resistant material
More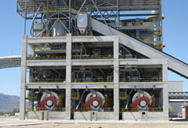
Surface modification of silica powder by mild ball milling
2022年11月5日 Fuji et al. reported that the powder surface can be activated by a mild ball milling treatment at very low rotation speeds without sufficient pulverization and silane coupling agents [17].The cleavages of siloxane bonds (Si–O–Si) on the silica particle surface could be confirmed because of the friction between the balls and particles even under mild milling, resulting in the
More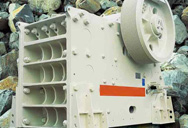
Ball charge optimization - INFINITY FOR CEMENT EQUIPMENT
Previous Post Next Post Contents1 Ball charge optimization2 1 How to use the BP2.1 2 Description of the main indicators used in this BP2.1.0.1 The residue on 2mm/4mm before partition wall2.1.0.2 Material filling level and ball charge expansion2.1.1 Cement mill specific power 1st compartment 2.1.2 Raw mill specific power 1st compartment Ball charge
More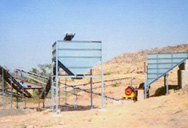
Ball Mill Rod Mill Design - 911Metallurgist
2016年4月22日 The apparent difference in capacities between grinding mills (listed as being the same size) is due to the fact that there is no uniform method of designating the size of a mill, for example: a 5′ x 5′ Ball Mill has a working
More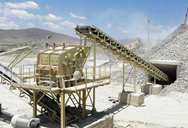
Optimization of Particle Size and Specific Surface Area of Pellet
2016年11月25日 It was found that for samples having equal Blaine specific surface areas numbers, the amount of fine particles produced in HPGR was higher than that produced in a ball mill. A higher surface area ...
More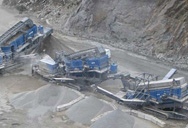
Tips on surface milling with ballnose endmills. HSM Machining
2013年11月18日 When surface-milling you often need to first rough, then semi-finish then finish. Leave 15 thou after roughing, 3 thou after semi-finishing, and finish to zero. All with progressively smaller tools. 5 thou stepover will give you a good finish on most ball mills; 3-5 thou chiploads are very common for finishing surface finishing. When shallow ...
More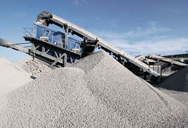
Ball Nose Surface Finish - WIDIA
All 0°/90° High-Speed Cutting Mills ; VHSC Series ; Helical Mills . All Helical Mills ; VSM11 Series ; VSM17 Series ; M300 Series ; M390 Series ; Slotting Mills . All Slotting Mills ; M900 Series ; M16 Series ; M94 Series ; M95 Series ; High-Feed Mills . All High-Feed Mills ; VXF™ Series ; M370™ Series • High-Feed Double-Sided Platform ...
More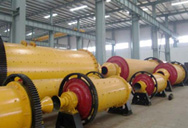
Ball Mill PPT - SlideShare
2015年11月30日 A ball mill consists of a hollow cylindrical shell that rotates about its axis, with balls occupying 30-50% of the volume to facilitate grinding as the shell rotates. Applications of ball mills include grinding metallic powders, carbon, coal, cement, fertilizers and other materials. Read less
More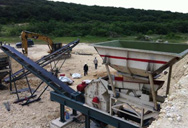
Trunnion Bearing Assembly Ball Mill Rod Mill - 911Metallurgist
2015年7月28日 Ball Mill PINION SHAFT BEARINGS. Pinion shaft bearings are of the SKF anti-friction type mounted in a common twin bearing assembly. Bearings are fixed in place so that the pinion shaft of the mill is always in alignment with the drive components. V-belt driven mills are furnished with an outboard bearing of similar construction.
More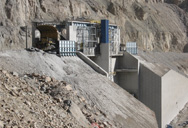
A comparison of wear rates of ball mill grinding media
2016年1月1日 The Ball Mill Abrasion (BMA) ... ball surface, but also on the surfaces of cross-sectional slices, which may also be used for . inspection of microstructure and internal . defects.
More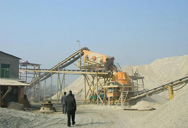
BALL MILLS Ball mill optimisation - Holzinger Consulting
Ball mills and grinding tools Cement ball mills are typically two-chamber mills (Figure 2), where the first chamber has larger media with lifting liners installed, providing the coarse grinding stage, whereas, in the second chamber, medium and fine grinding is carried out with smaller media and classifying liners.
More>> Next:Image De La Machine Du Recepteur De Concasseur A Machoires