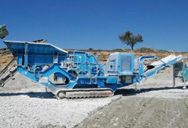
Modeling of energy consumption factors for an industrial cement ...
2022年5月9日 SHAP analyses highlighted that working pressure and input gas rate with positive relationships are the key factors influencing energy consumption. eXtreme Gradient
More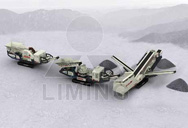
Benchmarking of Energy Consumption and CO2 Emissions in
Key energy and emissions parameters, including thermal and electrical energy intensity, recovered energy and CO2 intensity, are computed per tonne of cement produced along with
More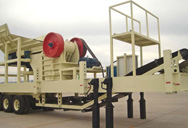
Energy consumption assessment in a cement production plant
2015年6月1日 Energy consumption assessment in a cement production plant is studied in this paper and a guideline for reducing energy consumption is provided according to a
More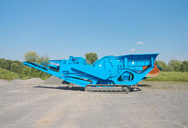
An overview of energy savings measures for cement industries
2013年3月1日 In this paper, energy saving measures in the cement industry, such as energy-efficiency measures for the preparation of raw materials, production of clinker, and the
More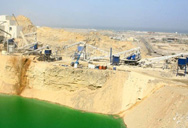
IMPROVING THERMAL AND ELECTRIC ENERGY EFFICIENCY AT
Cement accounts for at least 5 percent of anthropogenic emissions of greenhouse gases, and, according to some estimates, this share may be even higher. At the same time, energy
More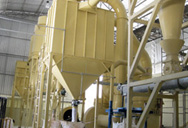
Energy consumption for cement production
JAPAN CEMENT ASSOCIATION. Energy consumption for cement production. As figure 1 shows, the thermal energy in exhaust gas from kilns and coolers is put to various uses including pre-calcination, drying of raw materials and
More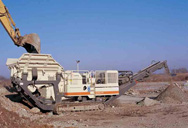
Benchmarking of Energy Consumption and CO2 Emissions in
2024年2月2日 Key energy and emissions parameters, including thermal and electrical energy intensity, recovered energy and CO 2 intensity, are computed per tonne of cement produced
More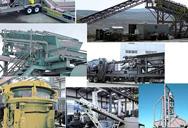
Optimization of Energy Consumption in Electric-Powered Modular
Abstract: Cement production is a critical industrial process that is inherently energy-intensive, contributing significantly to global carbon dioxide (CO2) emissions, with estimates indicating
More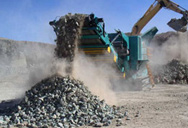
Optimization of Energy Consumption in Electric-Powered Modular Cement
Issue: The high energy consumption associated with cement production is directly linked to substantial greenhouse gas emissions. The combustion of fossil fuels for thermal energy in kilns is a major contributor to CO2 emissions, necessitating innovative solutions that decouple energy consumption from environmental impact.
More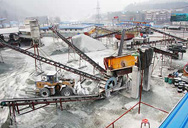
Energy-Efficient Technologies in Cement Grinding
2016年10月5日 In this chapter an introduction of widely applied energy-efficient grinding technologies in cement grinding and description of the operating principles of the related equip‐ ments and comparisons over each other in
More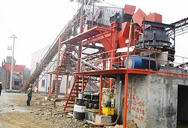
Optimizing Electrical Energy Consumption In Cement Process Plants
Cement Process Plants: Strategies For Energy Conservation And Sustainability M. Sarada Lecturer in Physics KVR Government College for Women (A), Kurnool, AP, India ... 20% of its rated output and thereby reduce the specific energy consumption. Addition of grinding aids may also increase the efficiency in clinker grinding.
More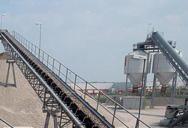
Cement Grinding Unit Cement Grinding Plant Cement Grinding
Cement grinding unit is a key link in cement plant. To achieve energy saving and consumption reduction in the cement industry, we must proceed from the cement grinding unit. Through a series of research and analysis, the following seven methods can effectively reduce the energy consumption of cement grinding plant. 1.
More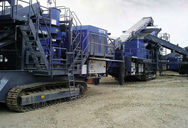
Energy consumption assessment in a cement production plant
2015年6月1日 In this paper, implementation of proper energy saving actions in an Iranian cement production plant was studied and several useful methods were suggested to improve energy consumption, since cement industry is considered to be one of the most energy intensive industries [7], [8].Establishment of proper saving actions is necessary to facilitate
More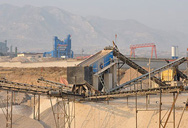
Benchmarking of Energy Consumption and CO2 Emissions in Cement
2024年2月2日 The research utilises industrial data from a 2850 tonne per day capacity dry process cement plant. Key energy and ... Adopting these BATs could reduce the electrical energy intensity of cement grinding by 30% ... Afkhami B, Akbarian B, Beheshti N, Kakaee AH, Shabani B (2015) Energy consumption assessment in a cement production ...
More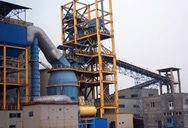
Energy consumption assessment in a cement production plant
2015年6月30日 The process of manufacturing cement is known to be an energy-intensive process; it involves the consumption of coal (fossil fuel), electrical energy, as well as other resources of energy, and this ...
More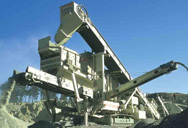
Cement Grinding - Cement Plant Optimization
Grinding Operation Objectives and KPIs. Chemical analysis of cement, generally on hourly basis. Product fineness, Blain surface and 45-micron residue. Cement SO3, % Grinding aid usage, grams/tonne Cement moisture, % Production rate, tonnes/hour Operating hours as run factor in % Specific power consumption (SPC) kWh/tonne.
More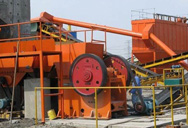
Review on energy conservation and emission reduction
2022年12月1日 The quality of the cement powder and energy consumption can be enhanced by improving the cement grinding circuits. Dry stirred milling is one such technology used in the cement industry. Altun et al. (2020) evaluated the applicability of this measure and found that by implementing this approach, 7–18% of energy can be saved with 2.8% of cement powder
More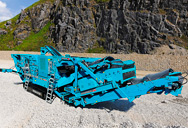
CEMENT GRINDING SYSTEMS - INFINITY FOR CEMENT EQUIPMENT
The final manufacturing stage at a cement plant is the grinding of cement clinker from the kiln, mixed with 4-5% gypsum and possible additives, into the final product, cement . In a modern cement plant the total consumption of electrical energy is about 100 kWh/t . The cement grinding process accounts for approx. 40% if this energy consumption.
More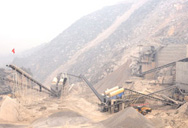
World Cement Grinding Milling QA
2022年2月18日 As well the consideration of production costs and carbon footprints, one key issue is energy consumption. For reference, the grinding process represents a significant part of a cement plant’s electrical demand, in
More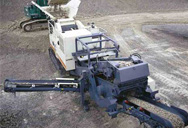
PERFORMING A CEMENT PLANT OPERATIONS AUDIT
Modern dry-process cement plants with an efficient grinding and pyro processing system, typically consume less than 700 kcal/kg-cl of thermal energy and 100 kWh/mt of electrical energy. Older plants with inefficient systems,
More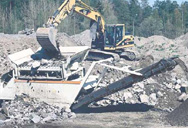
Energy-Efficient Technologies in Cement Grinding
2016年10月5日 In this chapter an introduction of widely applied energy-efficient grinding technologies in cement grinding and description of the operating principles of the related equipments and comparisons over each other in
More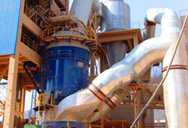
Reducing energy consumption of a raw mill in cement industry
2012年6月1日 While total electrical energy consumption for cement production is about 100 kWh/ton of cement, roughly two thirds are used for particle size reduction [2]. About 65% of the total electrical energy used in a cement plant is utilized for the grinding of coal, raw materials and clinker Fig. 1. Download: Download full-size image; Fig. 1.
More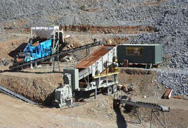
Process Training Ball Mill - INFINITY FOR CEMENT EQUIPMENT
Comminution is a major unit operation in a cement plant, accounting for about 50- 75 % of the total plant energy consumption. Fine grinding in general is extremely inefficient. The better mills on the market have an efficiency of about 8-9 % which means that only 8-9 % of the energy results in grinding and the majority is converted mainly into heat.
More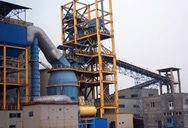
Energy consumption assessment in a cement production plant
2015年6月30日 The process of manufacturing cement is known to be an energy-intensive process; it involves the consumption of coal (fossil fuel), electrical energy, as well as other resources of energy, and this ...
More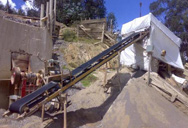
Benchmarking of Energy Consumption and CO2 Emissions in Cement
tonne per day capacity dry process cement plant.Key energy and emissions parameters, including thermal and electrical energy intensity, recovered energy and CO 2 intensity, are computed per tonne of cement produced along with capacity utilisation across major process stages including raw material grinding, clinkerisation and cement grinding.
More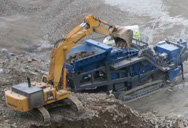
Fives FCB selected by EQIOM for the upgrade of its cement grinding ...
2024年9月9日 EQIOM was planning to upgrade its cement grinding plant with the installation of a latest generation classifier, aiming at improving separation performances to produce cement at a higher fineness with lower energy consumption levels. The projects ultimate goal is to reduce the clinker factor of the cement and its CO 2 footprint.
More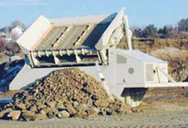
Sindri Cement Works - Green Business Centre
2.Specific Electrical Energy Consumption for last three financial years Plant Overall Specific Energy Consumption: Specific Electrical Energy Consumption: FY-Year 2020-21 2021-2022 2022-23 kWh/Ton Of cement 38.56 38.89 37.73 % Reduction 2.15% from 2020 -21 3.08% from 2021 22 38.56 38.89 37.73 37.5 38 38.5 39 2020-21 2021-22 2022-23
More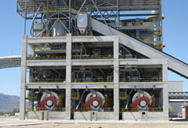
Monitoring global cement plants from space - ScienceDirect
2024年3月1日 Spatially explicit monitoring of global cement plants plays a crucial role in understanding global economic dynamics, assessing air pollution, analyzing energy consumption patterns, and formulating effective policies to mitigate CO 2, SO 2, and NO x emissions (Andrew, 2018; Bekun et al., 2022; Lei et al., 2011; Li et al., 2020).However, the
More>> Next:Concasseur De Charbon Européen