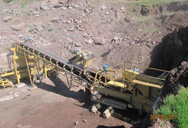
BALL MILLS Ball mill optimisation - Holzinger Consulting
Cement ball mills are typically two-chamber mills (Figure 2), where the first chamber has larger media with lifting liners installed, providing the coarse grinding stage, whereas, in the second chamber, medium and fine grinding is carried out with smaller media and classifying liners.
More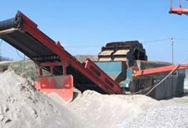
(PDF) Grinding Media in Ball Mills-A Review - ResearchGate
2023年4月23日 One of the most used tumbling mills is the ball mill. This paper reviews different types of grinding media that have been developed and improved over the years and
More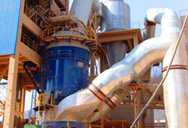
Ball Mill Success: A Step-by-Step Guide to Choosing
2024年8月8日 Unlock the secrets to ball mill efficiency with our comprehensive guide on choosing the right grinding media. Learn how material composition, size, shape, hardness, and cost impact your milling process and outcomes.
More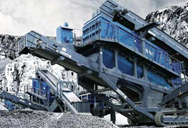
Predicting liner wear of ball mills using discrete element method
2022年6月1日 The liner wear of ball mills has been investigated based on the discrete element method and a data-driven approach. A new approach was proposed to predict the worn liner
More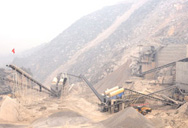
Three factors that determine the wear life and performance of mill
Ball mill Most ball mills, even in primary applications, have a finer ore feed size; this requires some impact but not enough to increase the media consumption or even break the liners.
More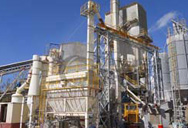
A Review of the Grinding Media in Ball Mills for Mineral Processing
2023年10月27日 Factors that influence the grinding efficiency include mill design, liner design, mill speed, mineralogical composition of the ore, charge ratio, and grinding media properties .
More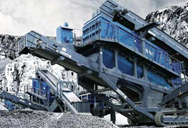
Grinding in Ball Mills: Modeling and Process Control - Sciendo
There are three types of grinding media that are commonly used in ball mills: • steel and other metal balls; • metal cylindrical bodies called cylpebs; • ceramic balls with regular or high
More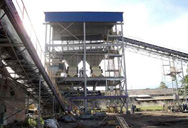
Modeling of the planetary ball-milling process: The case study of ...
2016年8月1日 A numerical dynamic-mechanical model of a planetary ball-mill is developed to study the dependence of process efficiency on milling parameters like ball size and number,
More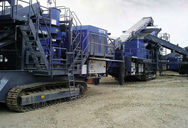
FLS Advanced mill liner wear measurement and prediction services
Add into the mix our advanced 3D scanning, liner profiling, and wear prediction technologies and you have a winning package. We make wear measurement simpler and faster – while keeping
More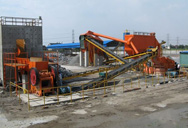
Ball Mill Liner Design - 911Metallurgist
2016年1月5日 End liners for ball mills conform to the slope of the mill head and can be made of rubber, alloyed cast steel or wear resistant cast iron. To prevent racing and excessive wear end-liners for ball mills are furnished with
More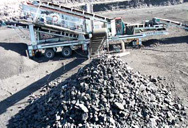
Ball Mill Grinding Machines: Working Principle, Types, Parts ...
Mill Liners: Liners protect the mill shell from wear and facilitate the movement of grinding media. They are typically made of rubber, metal, ... Ceramic Industry: Ball mills are extensively used in the ceramic industry for grinding and blending ceramic powders, glazes, ...
More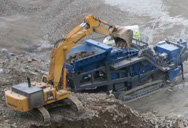
Calculation method and its application for energy consumption of ball
mills in a real ceramic manufacturing plant showed that the proposed calculation models could achieve an accuracy of more than 96% for predicting the ball mill energy consumption
More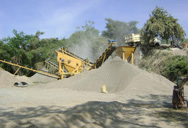
Ball Mill Efficiency Guide: Calculating Optimal Number Of Balls
2024年2月28日 Dive into the specifics to elevate your ball mill efficiency. 1. Mill Volume Analysis. The volume of your ball mill sets the stage for efficient milling. Calculate it by multiplying the total mill volume, accounting for void spaces, by the fraction filled by the balls. Typically, aim for a filling fraction between 30% and 50%. 2. Ball Mass ...
More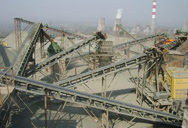
Ball Mill Linings - Multotec
Ball mill liner components: Our ball mill liners solutions can be fitted with MultoMet composite lifter bars, shell plates and head plates. The MultoMet range utilises Hardox 500 wear-resistant steel attached to the leading edges of the lifter bar array and embedded within shell plates and head plates, ensuring maximum abrasion and impact resistance.
More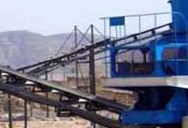
Grinding Media in Ball Mills-A Review - Academia
The ball mill is a rotating cylindrical vessel with grinding media inside, ... liner design, mill speed, mineralogical composition of the ore, charge ratio, and grinding media properties [5]. ... inert grinding media such as ceramic ball or pebbles have
More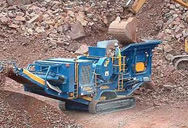
Comparing 2-in-1 Ceramic-Rubber Liners and Rubber Liners in Ball Mills ...
2024年10月15日 Both rubber liners and 2-in-1 ceramic-rubber liners play vital roles in ball mill operations, depending on the nature of the materials being processed and the specific operational needs.
More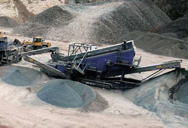
Charge behaviour and power consumption in ball mills: sensitivity
2001年8月1日 Fig. 2 shows the variation of the average torque and power with mill speed for the ball mill described above with a fill level of 50%. The torque increases slowly until the peak is attained around N=80%.As the amount of cataracting increases, the balance of the charge improves and the torque required to maintain the asymmetric charge position declines steadily.
More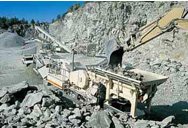
Ceramic Ball Mill For Sale – Automatic Ceramic Ball Mill
It is a kind of industrial ball mill that the liner plate is made of wear-resistant ceramics. AGICO manufactures automatic ceramic ball mills with low energy consumption. Skip to content [gtranslate] info@ballmillmachines +86 13683722138. Home; Ball
More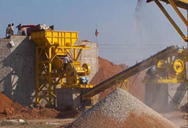
Predicting liner wear of ball mills using discrete element method
2022年6月1日 There are many experimental studies on liner wear, and various approaches have been proposed and implemented to increase the liner life (Banisi and Hadizadeh, 2007, Yahyaei et al., 2009).In particular, based on an experimental study, a liner wear apparatus was developed to monitor the liner wear effect on the grinding performance of ball mills (Powell,
More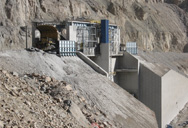
Ball Mill Liners - Made-in-China
China Ball Mill Liners wholesale - Select 2024 high quality Ball Mill Liners products in best price from certified Chinese Cement Interlock Bricks manufacturers, ... Durable Factory Grade High Silica Ceramics Ball Mill Liners. US$ 375-550 / Ton. 1 Ton (MOQ) Dalian Gaoteng International Trading Co., Ltd.
More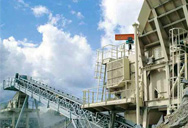
(PDF) Power consumption management and simulation
2022年3月15日 Various operational parameters, such as mill speed, the ball charge composition, charge filling, lifter type, and lifter number, significantly impact ball milling grinding efficiency [3].
More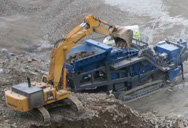
Calculation method and its application for energy consumption of ball
mills in a real ceramic manufacturing plant showed that the proposed calculation models could achieve an accuracy of more than 96% for predicting the ball mill energy consumption
More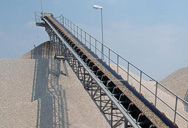
Calculate and Select Ball Mill Ball Size for Optimum Grinding
2013年8月3日 In Grinding, selecting (calculate) the correct or optimum ball size that allows for the best and optimum/ideal or target grind size to be achieved by your ball mill is an important thing for a Mineral Processing Engineer AKA Metallurgist to do. Often, the ball used in ball mills is oversize “just in case”. Well, this safety factor can cost you much in recovery and/or mill
More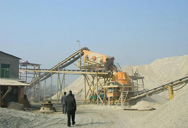
BALL MILLS Ball mill optimisation - Holzinger Consulting
Ball mills and grinding tools Cement ball mills are typically two-chamber mills (Figure 2), where the first chamber has larger media with lifting liners installed, providing the coarse grinding stage, whereas, in the second chamber, medium and fine grinding is carried out with smaller media and classifying liners.
More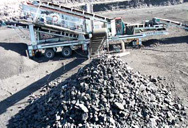
Ball Mill Grinding Machines: Working Principle, Types, Parts ...
Mill Liners: Liners protect the mill shell from wear and facilitate the movement of grinding media. They are typically made of rubber, metal, ... Ceramic Industry: Ball mills are extensively used in the ceramic industry for grinding and blending ceramic powders, glazes, ...
More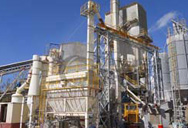
3 Types of Grinding Media for Ball Mills - FTM Machinery
2019年12月4日 When the speed of the ball mill is fixed and the ball loading is 30% of the total capacity of the cylinder, the ball’s movement is mainly sliding, but it has begun to pour. When the ball load exceeds 40%, the ball is pouring; When it reaches 50%, the surface of the ball is just on the diameter line of the cylinder, so it is easy to pour which is exactly needed for ball mill
More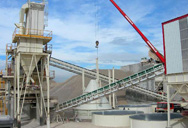
FLS Advanced mill liner wear measurement and prediction services
Advanced mill liner wear measurement and prediction services 3 FARO laser scanner Recording liner profiles as 3D cloud point data inside the . mill chamber. Our advanced liner profiling and scanning services use cutting-edge . technology to give you the most accurate and actionable information . about the condition of your mill liners.
More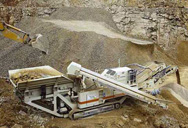
Ceramic Ball Mill for Sale Buy Ceramic Ball Mill Machine with
The ceramic ball mill uses a ceramic material liner, and ceramic alumina balls are used as grinding media. It is the key ball grinding mill equipment for fine grinding after the ceramic glaze is coarse grinding. The ceramic ball mill machine is widely used for the dry or wet grinding of the ceramic glaze mineral raw materials, such as feldspar, quartz, talc, kaolin, etc.
More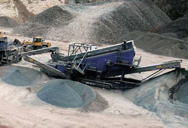
Charge behaviour and power consumption in ball mills: sensitivity
2001年8月1日 Fig. 2 shows the variation of the average torque and power with mill speed for the ball mill described above with a fill level of 50%. The torque increases slowly until the peak is attained around N=80%.As the amount of cataracting increases, the balance of the charge improves and the torque required to maintain the asymmetric charge position declines steadily.
More>> Next:Convoyeur à Bande Biologique