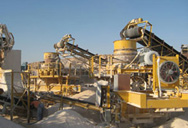
Direct reduction - Wikipedia
In the iron and steel industry, direct reduction is a set of processes for obtaining iron from iron ore, by reducing iron oxides without melting the metal. The resulting product is pre-reduced iron ore. Historically, direct reduction was used to obtain a mix of iron and slag called a bloom in a bloomery. At the beginning of the 20th century, this process was ab
More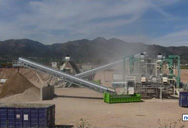
Sponge iron reaction - Wikipedia
The sponge iron reaction (SIR) is a chemical process based on redox cycling of an iron-based contact mass, the first cycle is a conversion step between iron metal (Fe) and wuestite (FeO),
More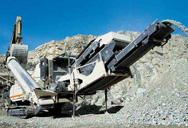
SLRN process - Metso
As an answer to decreasing ore grades, availability of lump ore and ever-increasing amount of fine ores and concentrates, Metso has developed a variant of the process, the SL/RN-Xtra
More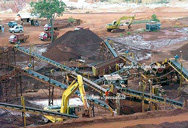
SL –RN process
SL-RN process. The SL-RN process was developed in 1964 out of the combination of two separate processes: the Stelco ¬–Lurgi (SL) (for process beneficiation high grade ores) and
More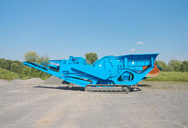
Direct Reduction Ironmaking - SpringerLink
2023年10月9日 It is the process in which high-temperature reducing gas and solid reductant are used to reduce iron ore in order to produce sponge iron. In the Midrex process, which is a
More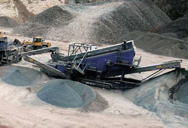
The SL/RN Process For Production of Metallized Burden - Springer
SL process was utilized exclusively for the production of sponge iron from high-grade iron ores for use in steelmaking furnaces. As far as low grade iron ores are concerned, the requisite
More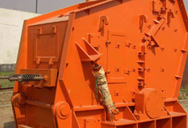
ENERGY-EFFICIENT TECHNOLOGY OPTIONS FOR DIRECT
India is the largest producer of direct reduction of iron (DRI), popularly known as sponge iron and accounted for about 39.3% of the global production in 2020. India’s growing economy will
More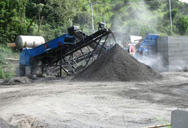
HYL III and SL/RN - The two widely accepted Direct Reduction (DR ...
2009年10月10日 SL/RN and HYL are two such DR processes. While HYL is a batch-type gas based process and uses a countercurrent shaft-furnace, the SL/RN process utilizes rotary
More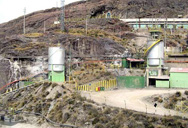
Haber process - Wikipedia
Fritz Haber, 1918. The Haber process, [1] also called the Haber–Bosch process, is the main industrial procedure for the production of ammonia. [2] [3] It converts atmospheric nitrogen (N 2) to ammonia (NH 3) by a reaction with
More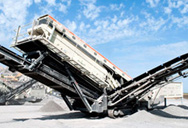
Iron - Wikipedia
Owing to environmental concerns, alternative methods of processing iron have been developed. "Direct iron reduction" reduces iron ore to a ferrous lump called "sponge" iron or "direct" iron that is suitable for steelmaking. [109] Two main
More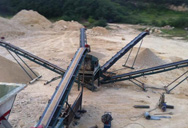
Soldering iron - Wikipedia
Electric soldering iron A gas-fired soldering iron. A soldering iron is a hand tool used in soldering.It supplies heat to melt solder so that it can flow into the joint between two workpieces.. A soldering iron is composed of a heated
More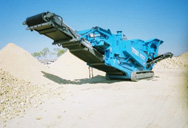
A REVIEW OF IRONMAKING BY DIRECT REDUCTION PROCESSES:
2023年11月10日 SLRN process. SLRN direct reduction process flowsheet @Hassan Harraz 2023 . IRONMAKING By DR Process. 21. 3. ... (DRI) or Sponge Iron. Processes that produce iron by reduction of iron ore ...
More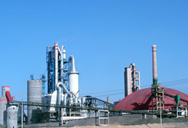
ENERGY-EFFICIENT TECHNOLOGY OPTIONS FOR DIRECT REDUCTION OF IRON PROCESS
Direct Reduction of Iron Process (Sponge Iron Plants). New Delhi: The Energy and Resources Institute Published by The Energy and Resources Institute (TERI) Darbari Seth Block, IHC Complex, Lodhi Road, New Delhi – 110003. iii ENERGY-EFFICIENT TECHNOLOGY OPTIONS FOR DIRECT REDUCTION OF IRON PROCESS
More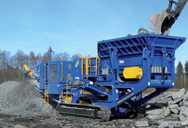
slrn process sponge iron wikipedia
2022-01-01T17:01:45+00:00; slrn process sponge iron wikipedia. Sponge iron reaction Wikipedia The sponge iron reaction sir is a chemical process based on redox cycling of an ironbased contact mass the first cycle is a conversion step between iron metal fe and wuestite feo the second cycle is a conversion step between wuestite feo and magnetite fe o in application
More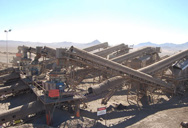
Direct reduction - Wikipedia
New Zealand Steel steel complex, fed by direct reduction rotary furnaces (SL/RN process) [1] (capacity 650,000 t/year). [2]In the iron and steel industry, direct reduction is a set of processes for obtaining iron from iron ore, by reducing iron oxides without melting the metal. The resulting product is pre-reduced iron ore.. Historically, direct reduction was used to obtain a mix of iron
More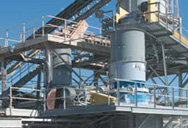
SLRN process - Metso
The process principles are the basis for numerous rotary kiln plants and still represent the dominant technology for the direct reduction of lump ore or pellets using coal. Operates with the widest range of iron-bearing materials, such as pellets, lump ore, beach sand, ilmenite and also iron ore fines with SL/RN-Xtra.
More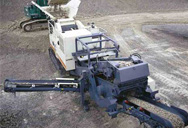
Future supplier of carbon dioxide-free sponge iron - LKAB
The shift towards carbon dioxide-free sponge iron begins in Gällivare, where our new demonstration plant will pioneer the industrial-scale implementation of the HYBRIT process. This milestone facility aims to yield around1-1.5 million tonnes of sponge iron annually.
More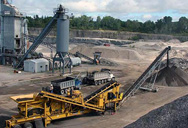
Cast iron - Wikipedia
Cast iron is a class of iron–carbon alloys with a carbon content of more than 2% and silicon content around 1–3%. [1] Its usefulness derives from its relatively low melting temperature. The alloying elements determine the form in which its carbon appears: white cast iron has its carbon combined into an iron carbide named cementite, which is very hard, but brittle, as it allows
More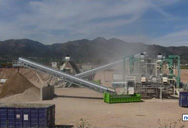
Which process is better for Sponge Iron Production?
A survey is made on a typical coal based Indian sponge iron plant of capacity 500 t/d in order to identify the largest energy losses and find ways to increase the efficiency.
More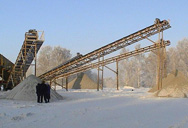
Rotary Kiln Manufacturers Electrotherm ET
Electrotherm ET is the foremost manufacturer of Coal Based Rotary Kiln for Sponge Iron (100 TPD, 350 TPD). Download Rotary Kiln PDF to get more product information. Our Products. Iron Steel Making. Coal based DRI
More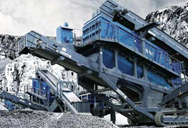
Iron and steel industry in India - Wikipedia
SAIL Steel Plant at Bokaro Steel City, Jharkhand a supersize steel plant- The second biggest steel plant in India, which contributes 45% of SAIL's profit . The Iron and Steel industry in India is among the most important industries
More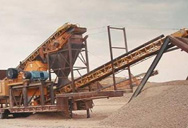
Pig iron - Wikipedia
Pig iron used to manufacture ductile iron. Pig iron, also known as crude iron, is an intermediate good used by the iron industry in the production of steel.It is developed by smelting iron ore in a blast furnace.Pig iron has a high carbon content, typically 3.8–4.7 %, [1] along with silica and other dross, which makes it brittle and not useful directly as a material except for limited ...
More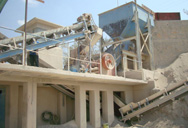
Sponge (tool) - Wikipedia
Vegetable fiber sponge: wood fiber sponge combined with scouring pad. Animal fiber sponge: A Greek natural sponge. A sponge (/ ˈ s p ʌ n dʒ / SPUNJ) is a cleaning aid made of soft, porous material.Typically used for cleaning impervious surfaces, sponges are especially good at absorbing water and water-based solutions.. Originally made from natural sea sponges, they
More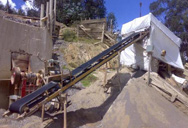
Sponge Iron - an overview ScienceDirect Topics
Direct reduction iron or sponge iron is an old method for producing hydrogen (Milne et al., 2006; Peña et al., 2010; Biljetina and Tarman, 1981) that was replaced by more efficient and economic processes.Recently, the interest in sponge iron as a hydrogen production process has grown again, although the technology still has some major technical and economic challenges to
More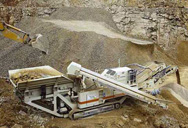
Direct Reduced Iron - IspatGuru
2013年12月14日 These standards are (i) ISO 4701:2019 Iron ores and direct reduced iron – Determination of size distribution by sieving, ISO 9686:2006 Direct reduced iron – Determination of carbon and/or sulphur – High frequency combustion method with infrared measurement, (iii) ISO 10835:2007 Direct reduced iron and hot briquetted iron – Sampling and ...
More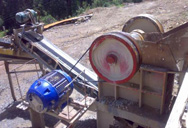
Iron Sponge - Oil Gas Process Engineering
2009年9月17日 The iron sponge process uses the chemical reaction of ferric oxide with H2S to sweeten gas streams. This process is applied to gases with low H2S concentrations (300 ppm) operating at low to moderate pressures (50-500 psig). Carbon dioxide is
More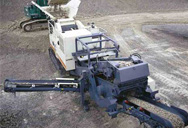
Future supplier of carbon dioxide-free sponge iron - LKAB
The shift towards carbon dioxide-free sponge iron begins in Gällivare, where our new demonstration plant will pioneer the industrial-scale implementation of the HYBRIT process. This milestone facility aims to yield around1-1.5 million tonnes of sponge iron annually.
More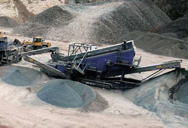
Design Procedures For Iron Sponge Unit - Oil Gas Process
2009年9月19日 The iron-sponge process generally uses a single vessel to contain the hydrated ferric oxide wood shavings. A drawing of an iron-sponge unit showing typical provisions for internal and external design requirements was presented in Figure 7-3.
More>> Next:Les Etats Financiers D Une Entreprise Moulin